How to Make Leak-Detection Soap
A leak in any gas piping system in your home, whether the pipes transport natural gas, propane or refrigerant, presents a serious problem. Gas leaks can result in explosions and fires, and refrigerant leaks can be environmental mini-disasters, depending on the age of your cooling system or refrigerator. It’s easy to detect leaks with a soap solution, provided the solution has the proper viscosity for bubbles to form.
It’s About Surface Tension
Any child who has tried to blow bubbles knows about surface tension — the cohesive force between molecules at the surface of a liquid. The surface tension of water — while strong enough to provide secure footing for certain water bugs — is too weak to make lasting bubbles, while that of liquid soap is too strong. The best bubble-blowing solution combines soap and water.
To detect gas leaks, you have to combine them in approximately the same ratio that a child would use to blow bubbles, but with maybe a little less soap, because the pressure a gas leak produces is usually less than that produced by a child blowing bubbles.
Bubble Recipe for Leak Detection
The Exploratorium website offers two recipes for bubble-blowing formulas, using two different dishwashing detergents. The recipes are similar and can be combined into one that will work using a generic dishwashing detergent:
- Fill a quart jar with clean water.
- Measure and add 3 tablespoons of dish detergent.
- Add 2 teaspoons of liquid glycerin to make the bubbles last longer, which makes them easier to detect.
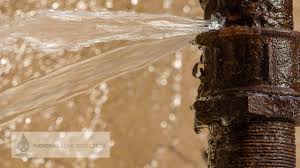
Leak detection and location survey
This case study describes leak detection and location activities carried out by one water company, following analysis of nightline data. It highlights how a leak detection survey is complemented by daytime location, and discusses the relative advantages and disadvantages of daytime and night sounding.
Sounding at night
This technique is practised mainly in urban areas. The company uses six-man teams of “night surveyors” who carry out a sounding survey. Each team surveys sluice valves, fire hydrants and stop taps equivalent to about 2500 properties per week (including time for gaining access to chambers). All leak sounds discovered during the night survey are passed to a core of skilled daytime inspectors who carry out full leak location. The use of night teams for surveying only has the following advantages:
- less ambient noise at night (easier to identify leak sounds);
- less customer use (fewer draw-off sounds);
- leak sounds are checked twice, once at night and once during the day (confirming leaks rather than use);
- night teams are dedicated to sounding survey and not leak location (survey rate maintained at 2500 properties per week);
- the day team is fully utilized in leak location rather than detection surveys (better use of skills and equipment);
areas with high volumes of road traffic can be surveyed at night, followed by the location team in the early hours of the same morning (eliminates the need for work on accumulated leaks, usually carried out in the early hours of Sunday morning).
Daytime leak location
It is not always practicable to use night survey teams, e.g. when there are few access points in the network, as in some rural areas. Other methods of leak detection and location are used in these circumstances, such as:
- correlation surveys on lengths of main;
sounding of distribution fittings by day inspectors;
use of acoustic data loggers which can be deployed as required.
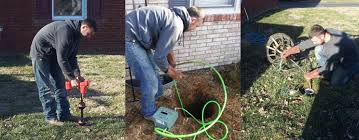
ACOUSTIC WATER LEAK DETECTION EQUIPMENT
The most effective way to find leaks in underground water pipes is with acoustic water leak detection equipment. This technology is based on the principal that as water escapes through the leak a mechanical vibration is generated and this vibration is audible with acoustic water leak detection equipment. When there is no pressure in the pipe because it is partially full or there is a complete rupture, a mechanical vibration is not generated and the leak cannot be detected acoustically. Different acoustic water leak detection equipment is used in the three stages of active leakage control designed for water distribution networks by the International waterloss taskforce, localisation, location and pinpointing.
Leak localisation
If the water network is managed in districts and minimum night flow data is monitored to identify rises in leakage the leak positions can be localised with step testing, listening to each service connection with a listening stick or using leak noise loggers. Because step testing and listening stick surveys are labour intensive and often require night work, leak noise loggers are usually the favoured option. It is not necessary to have the network sectioned into manageable districts to commence an active leak detection program however this minimum night flow data helps with the prioritisation of resources, understand the rate of rise (leakage) and performance of the network.
Leak location
When the leak position has been localised to section of pipe about 100 meters long (or less), leak noise correlators are used to locate the leak position. Transmitting acoustic sensors are deployed on valves, hydrants or exposed sections of the pipe either side of the leak position, pipe information between these two points is entered into the correlator and a peak is created on the correlation screen showing the point with the loudest noise. If the leak is not the loudest noise, filters may enable the operator to reveal the leak position. The leak location provided by a correlator is often accurate to within 1 metre (or less) but if incorrect pipe information has been entered this error will be greater. The operator is often unaware about changes in materials or mixed materials for pipe repairs, so it is important to the pinpoint the leak with an acoustic microphone.
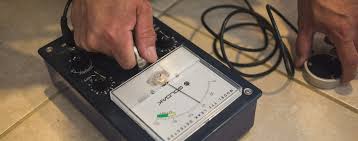
Pinpointing the leak
The path of the pipe should be marked on the ground and acoustic microphones are used to pinpoint the leak by identifying the point with the highest acoustic signal. On bitumen surfaces the operator can use a ground microphone or pocket microphone by placing them on the ground or they can drill or punch holes in the ground and insert a listening stick. On concrete slab the tripod foot or listening stick usually provide the best response, as a ground microphone is too sensitive. On grass or dirt the operator will get best results with the listening stick and punching holes with a T probe or plunger bar. If the ground is soft and water logged around the leak, the noise may actually be louder either side of the leak because the noise travels better through the compacted dry ground.
Residential and Commercial Leaks
The same principles of leak localisation, locate and pinpoint apply with leak detection in houses and the same acoustic water leak detection equipment is used. However the process is a little different. The Aquascope 3 acoustic water leak detection equipment and a pipe locator is generally all that is required unless there are very long sections of pipe when an Aquascan 610 leak correlator will speed up the leak location process. Use the electronic listening stick in the Aquascope 3 acoustic water leak detection kit to localise the leak position. Use a pipe locator to locate the path of the pipe and then use the Aquascope 3 to pinpoint the leak. There are three different acoustic microphones in the Aquascope 3 acoustic water leak detection equipment kit. For underground leaks in soft ground insert several probes and listen with the listening stick to pinpoint the position. Under concrete slab use the pocket mic or tripod foot to pinpoint the leak. Under a sealed surface use the ground microphone.
Tracer Gases
Working Principle
For those of you who might be wondering, a tracer gas is simply a gas that is not poisonous, colorless, odorless and unreactive. This gas can either be carbon dioxide, nitrous oxide, helium, sulphur hexafluoride or any other gas whose presence is detectable by use of a specialized gas detector.
Application
To detect a leak in your home, the system in question is first emptied of its contents. An ADI certified technician then introduces a mixture of two gases, hydrogen and nitrogen into the piping infrastructure at a safe pressure of 2 atmospheres. At the point where there is a leak in the piping, the tracer gas leaks out and is thus easily detected using a handheld gas detector. It is worth mentioning that this method is not as efficient in leak detection as the previous two methods. This method is over 99.5% accurate in leak detection.